xalax Autostore
Integrated in Microsoft D365
Two systems, one environment
Storage capacity and efficiency of the warehouse processes are the main drivers of operational excellence within a warehouse. Various hardware and software systems are used to optimize warehouse processes as much as possible. An increase in process efficiency is achieved primarily through a user-friendly system, i.e. when users move around in one environment and no system changes are necessary.
The best use and user experience of an AutoStore warehouse automation system is therefore achieved through full integration with Microsoft D365. A seamless material flow, combined with innovative warehouse technology, leads to the optimal application of a goods-to-man solution embedded in an ERP and/or warehouse management system.
Your benefits
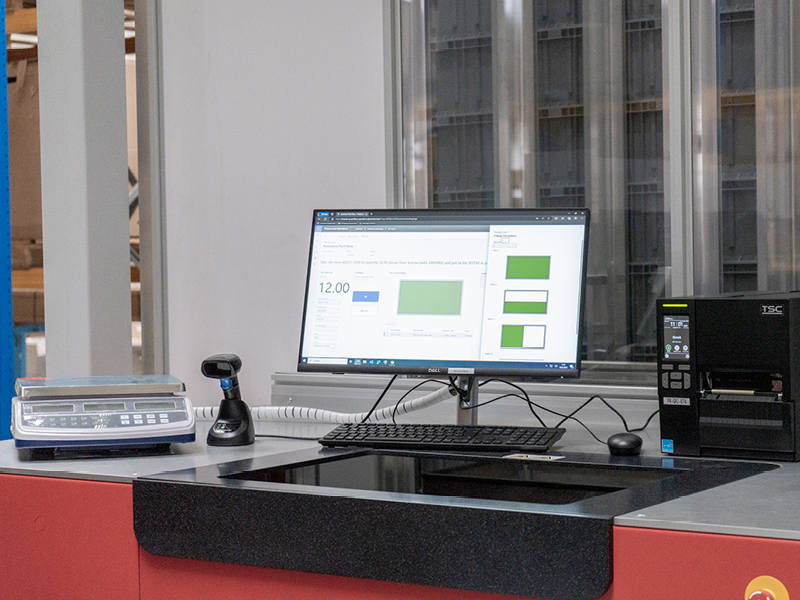
xalax is a certified AutoStore WMS Consultant and provides professional support for AutoStore integration into the Microsoft D365 environment and the implementation of the project.
By using the xalax Autostore module, the following goals are achieved:
- Direct communication between AutoStore and D365 (F&O)
- No 3rd party system, no middleware – AutoStore is no black box
- Two system, one environment
- One Guided User Interface
- Optimal material flow and increased efficiency of warehouse processes
- Redundancy and risk minimisation
- Optimization of operation, maintenance & support
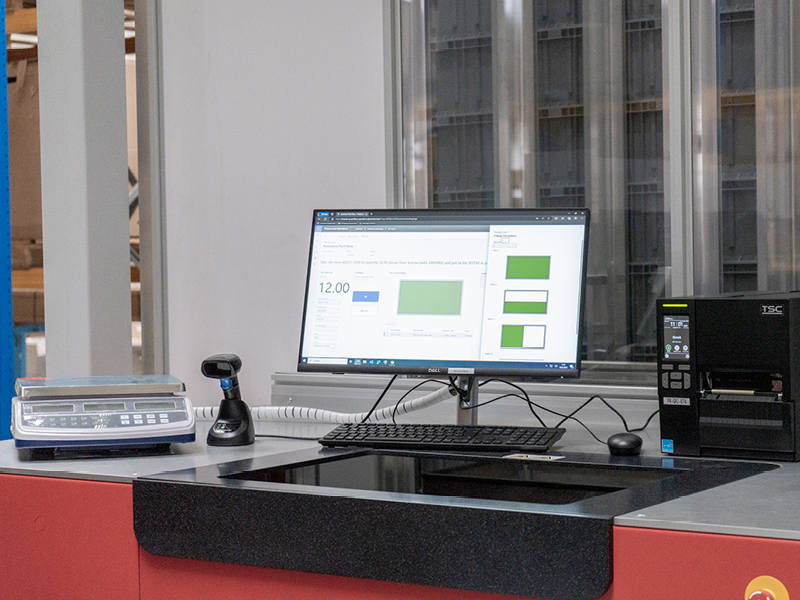
Deployment options
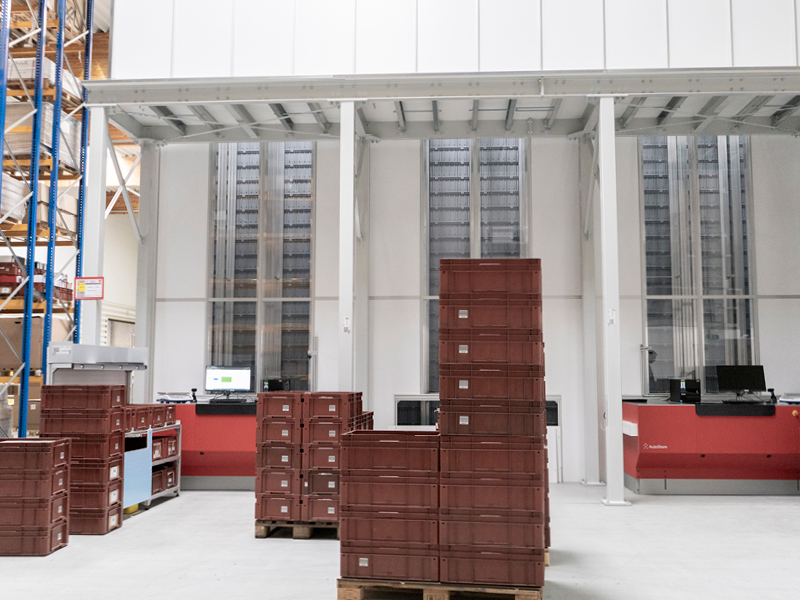
A continuous material flow is the top priority in the supply chain, which is why the xalax Autostore functionalities are also based on the core functionalities of the D365 warehouse management module. As the implementation of the xalax Autostore module requires the use of the D365 warehouse management module, two integration scenarios are possible depending on the customer's needs or existing environment:
- Integration into D365 Finance & Operations (F&O)
- Integration with D365 Warehouse Management Only Mode (WOM)
Customers who use Dynamics 365 Finance and Operations (D365 F&O or D365 F&SCM) as a cloud-based enterprise resource planning system choose the full integration of the Autostore module. The “Warehouse Management Only” mode, on the other hand, offers the option of using only the core SCM functionalities of D365 while other ERP and/or order management systems are in use, such as 3PL solutions and fulfillment logistics.
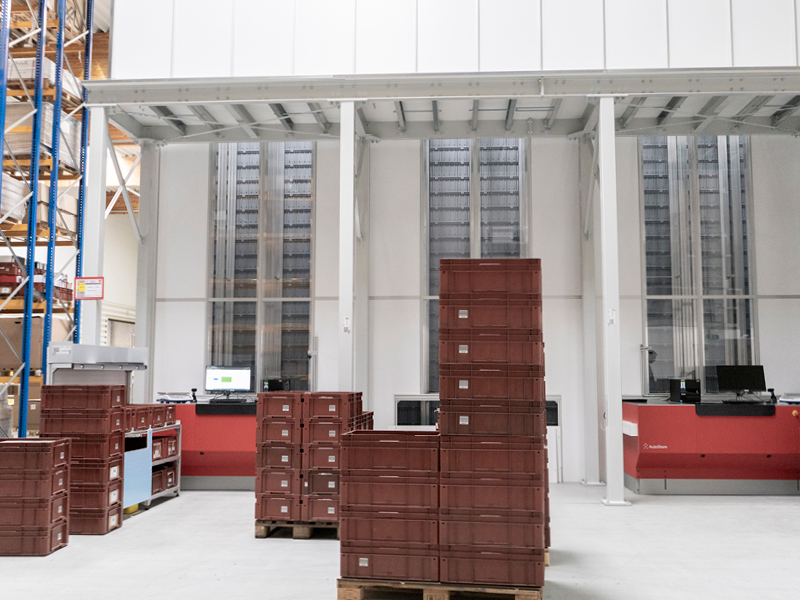
Processes
The basic idea of the AutoStore warehouse automation system is to store a large number of items in the smallest possible space and to pick them automatically in the shortest possible time. The xalax Autostore module contains all the functions required to control and carry out the work on the AutoStore execution system. The most important warehouse processes include inbound and outbound processes, as well as the cycle counting process and stock transfer.
Standard basic module
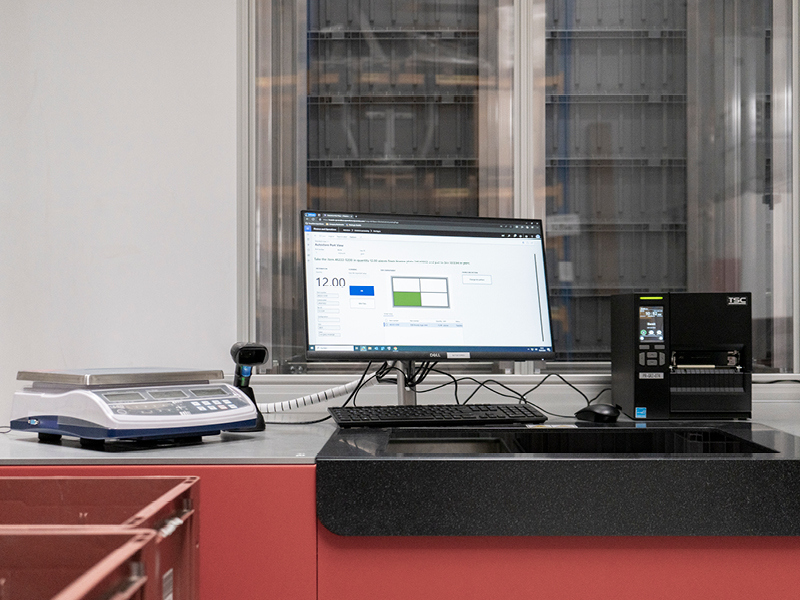
The standard xalax Autostore software package includes all the functionalities required to control and execute standard inbound, outbound, cycle counting and stock transfer works. The interface to the AutoStore warehouse automation system, the supervisor's control station as well as the front end of the port and the mobile device control are part of the basic module.
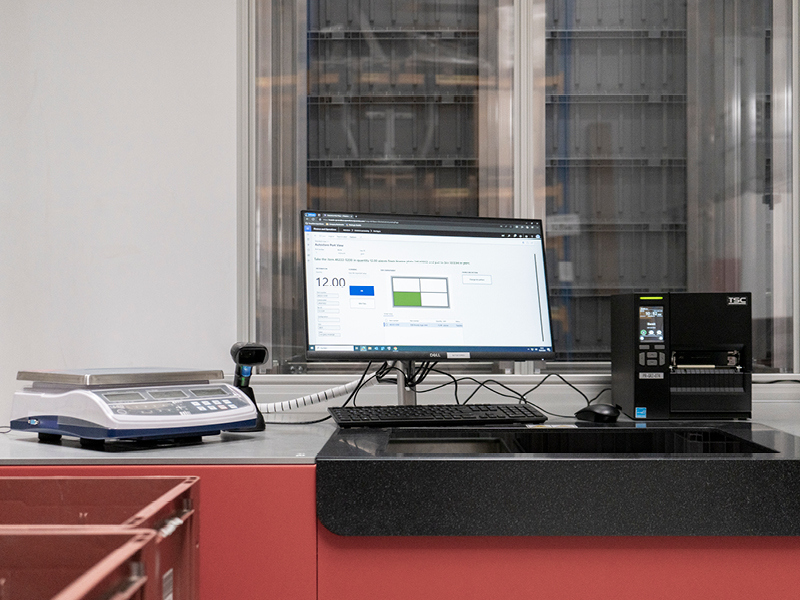
Interface to AutoStore
The interface streamlines the flawless communication between the D365 system and the automatic storage and retrieval system. AutoStore as the executing system receives “a list of bins” which need to be retrieved and brought to a specific workstation. Warehouse management and Autostore module do not control the stream of bins to workstations, the material handling system is doing this itself.
Port
The workstation for all the warehouse processes is the so-called port. The port is equiped with a screen and a hand-held scanner (MD – mobile device), which are controlled by the Autostore module. The operator working at the port is being guided by instructions on the screen. Depending on the design of the workstations and setup of the system, single ports can execute all or only defined logistical processes.
Control Center
Control operations as the port management or the supervisor view are available in the so called control center. The port management provides an overview of all available ports, with status and the possibility of opening or closing the individual ports, as well as setting the port mode (inbound, outbound, cycle counting), while as the supervisor overview provides a view of currently open orders per mode.
Inbound Process
The inbound process stores items into the AutoStore system. The items may come directly from the receiving area or from another storage location in the warehouse (e.g. overstock). The stating area is the starting point of the storing process into AutoStore. At the port the operator is instructed by the system, what quantity from which item should be put into a specific storage bin, which is retrieved by the system and brought to the port. The operator receives instructions step by step until all items are stored.
Outbound Process
When starting the picking process, the employee at the port receives the information to scan a new target license plate (empty container/carton/tote) and pick the specified quantity from the retrieved BIN and place the item(s) into the target container. This process can be repeated for multiple order lines. The operator sees on the Front-End, how many picking lines belong to a specific order. When an order is finished, the operator is instructed to put the license plate to the so-called AS-OUT location, which is the end-point of the outbound process.
Cycle Counting Process
The inventory cycle counting is a warehouse process that is used to audit on-hand inventory items stored in the AutoStore system. The cycle counting occurs continuously throughout the entire financial year. The assets are not recorded on a specific date, but at regular intervals. This way you are always informed about the current stocks of your materials and products.
Module enhancements
There are couple of hardware and software features, which are not part of the standard software package xalax Autostore, yet can be implemented as additional service. Find here some examples:
Hardware enhancements
Optionally, hardware or feature enhancements can be included as for example the control of Label Printer, Document Printer, Scale, Camera and Pick-to-Light / Put-to-Light.
Multi Order Picking
With the multiple order picking the same item can be picked from one single storage location/ bin for multiple orders, before the bin is stored back into the system. A rack with multiple put locations is located next to the port. The operator needs to assign an order (license plate) to one of the designated put locations prior to the picking process. The system informs the operator, where (which put location) to put how many units, and when an order is finished.
Pick & Pack
Sales orders, which are picked only from the AutoStore, can be prepared for shipping directly at the port. Due to correct item master data the size of the needed shipping container can be suggested. The system guides the worker through the whole picking process and closes the process off with a completed packing process. The shipping label and any other needed documentation (as packing slip, invoice etc.) is printed directly at the port.